Selecting the best portable air compressor for an application comes down to proper air compressor sizing as choosing an incorrectly sized unit will result in ineffective production and wasted resources. To help answer the question of “what size air compressor do I need?”, this blog will provide an air compressor sizing guide and discuss how to select an air compressor.
The Importance of Proper Air Compressor Sizing
Selecting a portable air compressor is not a one-size-fits-all situation. The chosen air compressor must provide enough power – in the form of pressure and airflow – to run the tools and equipment necessary to the application. If the portable air compressor is too small, it will not provide adequate airflow and pressure, which will result in poor equipment performance that has a negative impact on production. Insufficient sizing can also create a situation in which the portable air compressor is overworked, causing wear and tear or overheating of the motor or other components.
Conversely, if the portable air compressor is oversized for the application, it will use more energy than necessary, wasting resources such as electricity or gas, if it’s a portable gas air compressor.
For these reasons, understanding air compressor sizing is crucial to selecting the best portable air compressor for the application.
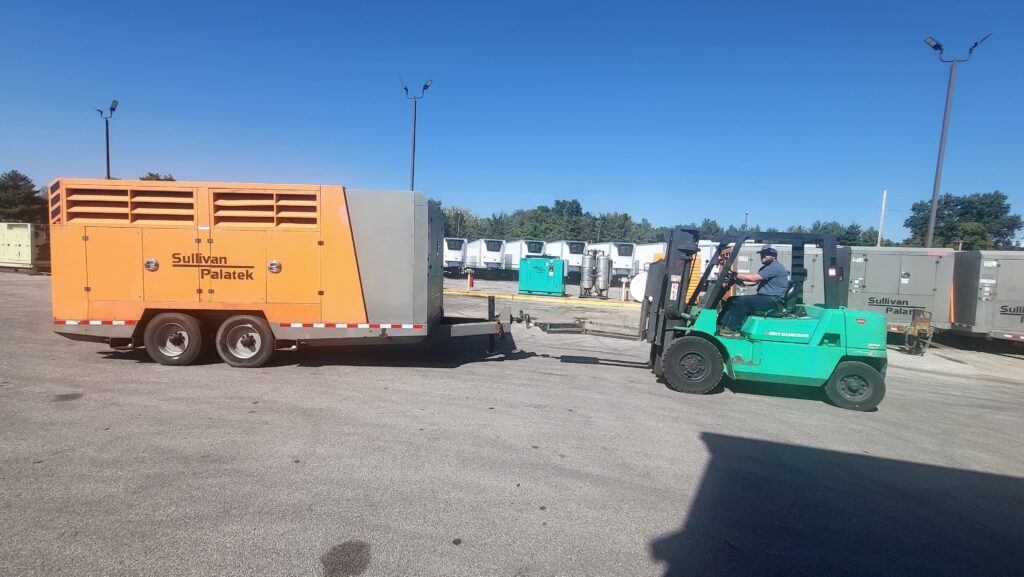
CFM and PSI: The Keys to Air Compressor Sizing
One of the biggest challenges when sizing a portable air compressor is understanding the necessary specifications and how they apply to an application. The most important selection and sizing criteria include the airflow and the pressure as these determine whether the portable air compressor can properly power the pneumatic tools at the site.
The airflow, or air volume, is typically expressed as cubic feet per minute (CFM). As a general rule of thumb, the higher the CFM rating of the compressor, the more powerful it will be. However, choosing the portable compressor with the highest CFM available is rarely the best choice. Rather, the best portable air compressor is the one that delivers the right CFM for the job as this will ensure optimal performance, efficiency and the longest life for the compressor.
To determine the proper CFM for air compressor sizing purposes, take the following steps:
1. Determine the CFM for each tool: Portable air compressors may be required to power several pneumatic tools and pieces of equipment at one time, so obtaining the manufacturer’s CFM specification for each tool will be necessary. If the CFM isn’t displayed on the tool or in the product manual, contact the manufacturer.
2. Calculate the minimum CFM requirement: Once you’ve determined the CFM for each tool, add all of them together and multiply that number by 1.5 to allow for surges that may occur with startups. This will be the minimum CFM requirement.
3. Calculate the total CFM requirement: While the minimum CFM requirement will comfortably get the job done, many experts suggest boosting the minimum CFM requirement by 25% to allow for peak demands and future growth.
A sample CFM calculation would look like this:
(CFM of all tools that will operate at the same time) X 1.5 = minimum CFM requirement.
So, if you have three tools with a CFM requirement of 10, the calculation would be as follows:
(10 CFM + 10 CFM + 10 CFM) X 1.5 = 45 minimum CFM requirement
And, if you want to add 25% to that number to permit peak demand, the recommended total CFM value would be 56 CFM.
(10 CFM +10 CFM + 10 CFM) X 1.5 = 45 X 125% = 56 total CFM requirement
However, air compressors are not just rated for a specific CFM, rather, they are rated for a particular CFM at a designated pressure or psi rating (for example, 100 CFM at 100 psi), which makes pressure, measured as pounds per square inch, or psi, the other key criteria when determining air compressors sizes.
To ensure that a portable air compressor will provide the best performance at the highest level of efficiency, it’s important that the unit can produce sufficient CFM at the right pressure for the application. To establish the psi requirement for the operation, simply use the psi value for the tool that demands the greatest amount of pressure.
How to Select an Air Compressor
Once you have determined the required CFM and psi values, ensure with your supplier that the portable air compressor you are considering can deliver the total CFM at the proper psi as the two values are necessary to providing efficient and effective operation of the pneumatic tools and equipment at the site.
While these are the most important considerations when sizing an air compressor, there are other selection criteria, including:
Power considerations | Both the horsepower and power supply are critical criteria when selecting a portable air compressor. The horsepower describes how much power the compressor’s engine can provide. Power supply options include electric, hydraulic and gas. The power supply will depend upon what is available at the job site where the portable compressor will be located. |
Tank size | Intermittent compressor usage can rely on small storage tanks, but if the portable compressor will be running continuously, it is important to select a unit with a larger tank to allow a constant supply of air. |
Duty cycle | The duty cycle expresses how often a compressor can operate before it must pressurize more air. A portable compressor with a 50% duty cycle would need two minutes to cycle in new air following one minute of run time. |
The air compressor sizing guide presented in this blog, along with other key selection criteria, should help you find the best portable air compressor for your application. However, if you need assistance with calculating the CFM and psi requirements to ensure proper air compressor sizing or help choosing a portable air compressor, please contact the experts at HTE, a Tavoron company.