The objective of an industrial conveyor system is to efficiently and reliably move products or materials through a facility. However, to successfully do so, the conveyor system must jive with the specifications of the application, the layout of the plant, the facility’s environment and the company’s overall business goals.
There are a lot of conveying options – from belt conveyors to pallet conveyors to modular conveyors – and conveyor belt types – from flat belt conveyors to cleated conveyor belts, so there is an industrial conveyor system to meet the requirements of any application. Therefore, understanding the precise specifications of the application, including the characteristics of the material or product being moved, the available footprint and the overall project goals, will simplify the selection process. This blog provides six important factors to consider when purchasing an industrial conveyor system, helping to ensure that the chosen system provides the required functionality and efficiency.
Types of Industrial Conveyor Systems
Before delving into conveyor selection considerations, we’ll provide a quick review of the most common industrial conveyor systems and conveyor belt types, including:
Roller Conveyors | The surface of this industrial conveyor system consists of rollers that are selected to match the weight and speed requirements of the product and application. Roller conveyors offer a simple, reliable and inexpensive method of transporting parts, products and packages. |
Flat Belt Conveyors | flat belt conveyors are also versatile, but the flat belt, which has no curvatures or troughs as a standard belt conveyor might, makes them most suitable for moving light- to medium-weight loads. They are simple in design and construction, which makes them an option for general manufacturing needs. |
Cleated Conveyors | Cleated conveyor belts feature belts with evenly spaced or strategically placed cleats or barriers to provide consistent space between products or to improve grip and facilitate movement up and down inclines while preventing large or loose products from falling out of place. |
Modular Conveyors | Modular conveyors use a single loop of interlocked pieces. They excel in applications that must travel around corners or those that require specific or unique conveyor layouts or designs. |
Pallet Conveyors | Pallet conveyors, which move large or heavy loads via belts, slats, rollers or chains, are usually positioned low to the ground for better control. Pallet conveyors are typically integrated with ancillary pallet handling equipment such as robotic palletizers and depalletizers, turntables, stretch wrappers, transfers and pallet dispensers. |
Incline/Decline Belt Conveyors | Incline/decline belt conveyors, or Z-frame conveyors, are used to transport materials and/or products to higher or lower elevations. |
Sanitary Stainless Steel Conveyors | Applications in the food and beverage and other sanitary industries often involve high temperature washdown procedures. Sanitary stainless steel conveyors are designed to withstand these procedures and provide a food-safe surface. |
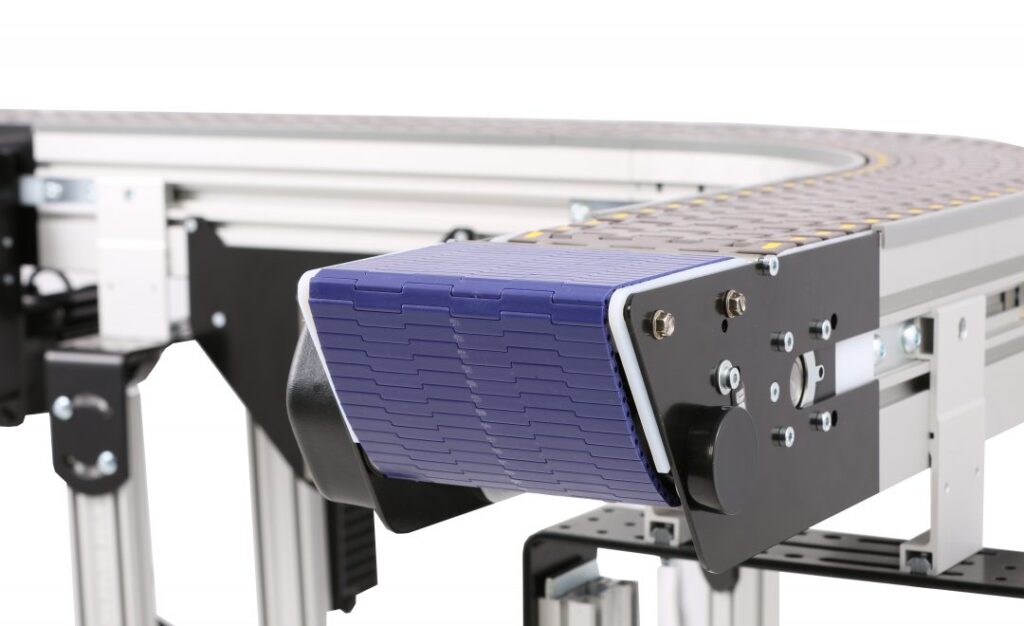
Dorner 3200 Modular Belt Conveyors
6 Considerations When Choosing an Industrial Conveyor System
Choosing the wrong industrial conveyor system can lead to inefficiencies, product damage, downtime and lost revenue, so it is crucial to dedicate some time to understanding the requirements of the conveying system during the selection process to ensure that the chosen conveyor will meet the specific demands of the application.
Below are six factors to consider when specifying an industrial conveyor system:
The application
Industrial conveyor systems are used for a multitude of applications, but can be narrowed down to two main operations: conveying (moving products from point A to point B) or feeding (feeding materials continuously or in batches into a process). Understanding the requirements of the application and intended function of the conveyor will help narrow down the choices.
Cost
Due to budget constraints, cost will always be a factor, but it should not be the most important one. While the conveyor system should fit within the budget and the calculation should include the cost of the equipment, as well as other project necessities such as design, installation and necessary renovations, it is often the case that spending more to install a durable and reliable industrial conveyor system that meets the needs of the operation, accommodates the characteristics of the products and will function in the environment is a worthwhile investment.
Available footprint
To provide the highest level of efficiency, the selected industrial conveyor system must fit well within the available footprint. For example, if there are obstructions, a modular conveyor may be the best choice. Or if space is very limited, an incline or overhead conveyor may be a better option. No matter what layout is planned, ensure that the conveyor system won’t interfere with other operations and that there is enough space around it to allow access for operators and maintenance technicians.
Special environments
Special considerations include open sources of ignition, potential for flammability or explosiveness, extreme temperatures, corrosive vapors or products, high humidity levels, vibration or pressures as these may combine with certain material characteristics to create a health and safety concern that must be addressed.
The products
Evaluate the specific features of the product the conveyor will be handling as this will impact the selection. Consider the product type, length, height, width and weight. Characteristics such as high-moisture content, flammability, temperature sensitivity, abrasiveness or fragility will further influence system requirements and may demand a specialized industrial conveyor system or conveyor belt type.
Business goals
An industrial conveyor system should align with the business goals to increase efficiency and improve the process. In addition to ensuring that the system will handle products without breakage, damage or safety incidents and can safely and effectively operate in the space and environment where it is installed at the required speed and efficiency level, it is also important to consider whether the business plans to expand in the future, in which case a modular conveyor may be a good option.
The most effective industrial conveyor system will be one that meets all the specifications of the application without presenting safety hazards, inefficiencies, product damage or other issues that will minimize the success of the operation. Talking with the experienced representatives at HTE, a Tavoron company, will ensure that you’re purchasing a suitable conveyor that will reliably move products in a way that increases throughput and profits.